Design of a mini CHP plant
Table of contents
Designing a mini-CHP (mini-heat and power plant) is a multi-stage process, including analysis of current conditions at the enterprise, development of technical solutions, preparation of project documentation and execution of approvals. This article will help you understand why it is necessary to design a mini-CHPP, what stages of design are forthcoming, what data should be collected, as well as how to assess the economic efficiency of the project. This is important because a properly designed mini-CHP ensures long-term savings, energy independence and control of energy supply costs.
Basic design terms and definitions
Mini-CHP (mini combined heat and power plant) is a compact power plant that provides the enterprise with electricity and heat, reduces energy supply costs and increases energy independence.
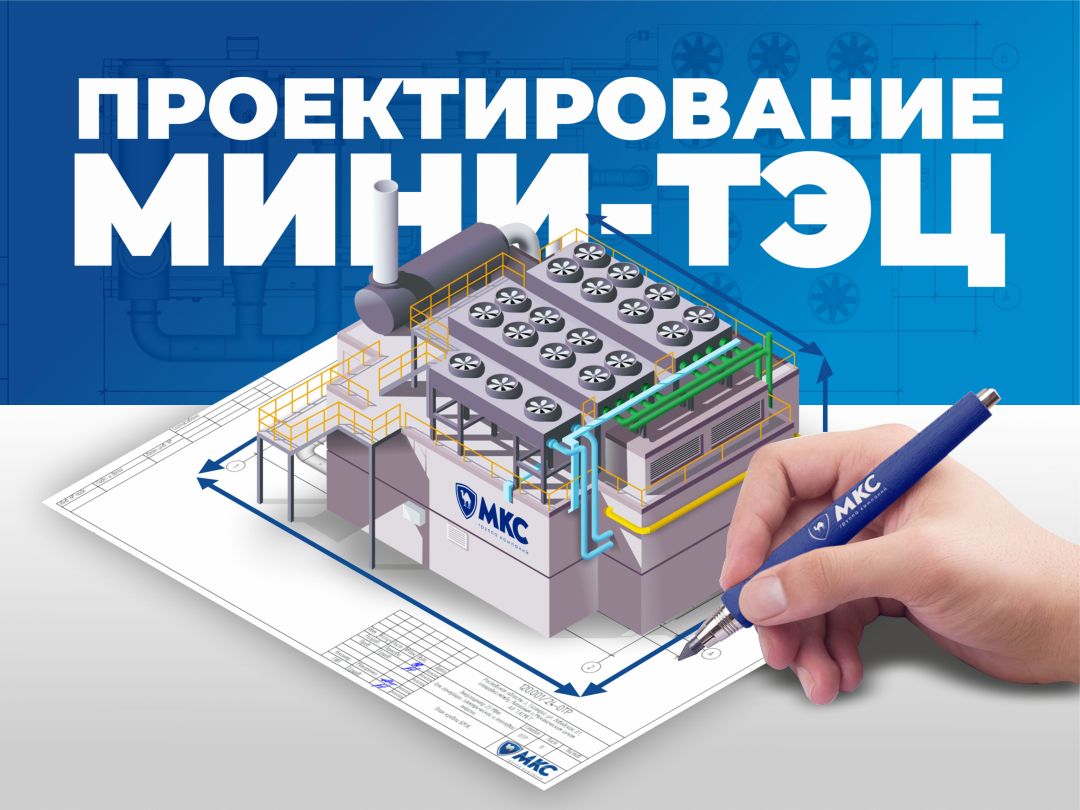
Design Stages
Table of main stages of mini-CHPP design
№ | Design stage | Objective | Main types of work | Result |
1 | Pre-project survey | Collection of initial data, assessment of the technical and economic feasibility of constructing a mini-CHP plant | - Specialist visit to the site - Engineering surveys (geology, geodesy, ecology, etc.) - Assessment of the connection point - Analysis of customer needs - Preliminary selection of equipment | Conclusion on the feasibility of the project, technical report, diagrams, and recommendations. Decision to proceed to the OTR stage. |
2 | Development and approval of the OTR stage (Main technical solutions) | Determination of the basic project concept and fundamental solutions for technological, electrical, and construction systems of the mini-CHP plant | - Development of technological process diagrams - Selection of main and auxiliary equipment - Network connection diagrams - Conceptual solutions for placement - Preliminary estimate | The document "Basic Technical Solutions" (BTS), agreed with the customer and key services. Transition to stage "P". |
3 | Development and approval of stage "P" (Project documentation) | Obtaining permits and passing expert review, ensuring compliance with regulations and standards | - Preparation of project documentation for 12 sections in accordance with Resolution No. 87 - Sections on EIA, fire safety, energy efficiency, etc. - Coordination with grid and gas distribution organizations | Complete set of project documentation (stage "P") approved by the customer and submitted for expert review. Transition to stage "R". |
4 | Development and approval of stage "R" (Working documentation) | Preparation of detailed documentation for the construction and installation of a mini-CHP plant | - Development of working drawings (KM, KZ, EOM, ATX, SS, etc.) - Specifications for equipment and materials - Installation plans - Load calculations, hydraulics, automation diagrams | Working documentation approved by the customer and accepted for construction. Transition to construction work and industrial safety expertise. |
5 | Industrial safety assessment | Obtaining a conclusion from Rostekhnadzor on the compliance of project documentation with industrial safety requirements | - Preparation and submission of a package of documents to the expert organization - Interaction with Rostekhnadzor - Elimination of experts' comments (if necessary) | Positive conclusion of the industrial safety assessment. Basis for starting construction and installation works. |
6 | Author supervision | Ensuring compliance of construction and installation works with project documentation | - Regular visits by the designer to the site - Verification of compliance of the works performed with the project - Keeping an author supervision log - Consultations and adjustments during the course of work | Confirmation of construction compliance with the project, closed author's supervision reports. The stage ends with the completion of construction. |
7 | Technical supervision (from the customer) | Quality control, deadlines, and scope of construction and installation works, compliance with construction standards | - Control of work performed by contractors - Checking the quality of materials - Participation in the acceptance of concealed works - Verification of as-built documentation | Technical supervision reports, signed acceptance certificates for stages of work. Continues until the facility is commissioned |
The stages of "development and approval of project documentation" and "author supervision" are variable and are carried out at the request of the customer.
Types of engineering surveys
At the pre-design survey stage, after the specialist has visited the site, engineering surveys are carried out.
Table with a detailed description of the various types of surveys required before the start of the design and approval stage of the OTR.
Survey direction | Purpose | Main types of work | Result |
Geodetic surveys | Accurate determination of site coordinates, recording of relief features, and creation of a topographic basis for design. | Topographic survey of the territory; determination of turning point coordinates; construction of plans and profiles of the terrain; creation of digital terrain models. | Topographic plan on a scale of 1:500 or 1:1000; data for foundation design and equipment placement. |
Geological surveys | Assessment of soil bearing capacity, groundwater depth, and calculation of foundation loads. | Drilling of engineering-geological wells; laboratory analysis of soil samples; determination of physical and mechanical characteristics of soil; study of seismic activity. | Geological report; data for foundation calculations and selection of building materials. |
Hydrogeological surveys | Determination of groundwater levels, their chemical composition, and impact on building structures. | Measurement of groundwater levels; analysis of water chemical composition; assessment of drainage and water disposal possibilities. | Hydrogeological report; data for the design of drainage systems and foundations. |
Climatological surveys | Assessment of climatic parameters affecting the reliability and efficiency of equipment. | Collection of meteorological data; analysis of seasonal fluctuations in temperature, humidity, and pressure; study of wind roses and precipitation. | Climatological report; data for the selection of thermal insulation materials and cooling systems. |
Environmental surveys | Determination of the project's impact on the environment, including emissions, noise, and vibrations. | Study of soil, air, and water conditions; assessment of noise and vibration levels; analysis of the impact on flora and fauna. | Environmental report; data for obtaining environmental permits and approvals. |
Technical surveys | Assessment of the condition of existing engineering networks and communications on the site. | Checking the condition of electrical networks; studying gas pipelines, water pipes, and sewer systems; analyzing the possibilities for connecting to external networks. | Technical report; data for designing engineering networks and selecting equipment connection schemes. |
The main stages of engineering surveys:
Field work | Conducting measurements and research at the construction site, drilling wells, installing benchmarks, taking soil and water samples. |
Desk work | Processing collected data, building digital models, calculating loads on the foundation, preparing reports. |
Analytical stage | Comparing the data obtained with standards, assessing potential risks and limitations, preparing recommendations for designers. |
Coordination and approval | Submitting reports to the customer, obtaining permits and approvals to continue design work. |
Results of engineering surveys:
Document | Contents | Purpose |
Topographic plan | A detailed map of the site showing the relief, existing buildings, utilities, and boundaries of the territory. | The basis for designing foundations, networks, and equipment placement. |
Geological report | Data on soil composition, strength, and water saturation, recommendations for foundation selection. | The main document for calculating building structures. |
Hydrogeological report | Information on the depth of groundwater, chemical composition, and possible impact on structures. | The main source of data for designing drainage systems and protecting foundations. |
Climatological report | Data on temperature regimes, wind speed, precipitation levels, and humidity. | The main document for selecting thermal insulation and cooling systems. |
Environmental report | Assessment of the facility's impact on the environment, noise and emissions levels, recommendations for reducing negative impact. | Required for obtaining environmental permits and approvals. |
Technical report | Description of the condition of engineering networks and communications, recommendations for their modernization and connection of new capacities. | Used to develop equipment connection diagrams and optimize power supply. |
Results of engineering surveys:
Conducting engineering surveys allows you to minimize the risks associated with choosing the wrong location for construction, increase the reliability of the foundation and engineering systems, and reduce equipment operating costs. This data is also necessary for obtaining building permits and connecting to utility networks.
Development of technical specifications (TS)
The development of technical specifications (TS) is one of the key stages in the design of a mini-CHP plant, which determines the main technical requirements for the facility, the functional parameters of the equipment, and the operating conditions. Properly drafted technical specifications significantly reduce design time, minimize the risk of errors, and ensure the high quality of the future energy complex.
Goals and objectives of developing technical specifications
Purpose of the technical specifications | Main tasks |
Determination of technical parameters of the facility | Establish the required power characteristics of the equipment, taking into account the specific features of operation in the specified climatic and geological conditions. |
Consideration of customer requirements | Reflect specific customer requirements, including restrictions on cost, implementation deadlines, and operational features. |
Optimization of energy efficiency | Ensure minimum specific fuel consumption, maximum efficiency, and flexibility of operation in various modes. |
Compliance with regulatory requirements | Take into account all applicable GOSTs, SNiPs, and safety rules for energy complexes. |
Creating a basis for design | Create a document that will serve as the basis for the development of design and working documentation. |
Main sections of the technical specifications
Section of the ToR | Description | Main Parameters |
General Information | General information about the facility, including its location, purpose, and main characteristics. | Name of the facility, address, purpose of creation, key indicators (capacity, area, number of employees). |
Technical Requirements | Main requirements for equipment, including electrical and thermal power, efficiency, type of fuel used. | Power (electrical and thermal), type of fuel, efficiency, reliability requirements, equipment lifespan. |
Connection Requirements | Conditions for connection to external utility networks, requirements for the quality of power supply. | Voltage level, current frequency, connection scheme, backup requirements. |
Operational Conditions | Description of operating conditions, including climatic features, requirements for resistance to external influences. | Temperature range, humidity level, resistance to vibrations and dust, noise level requirements. |
Safety and Environmental Friendliness | Requirements for operational safety, labor protection, and environmental protection. | Limitations on emissions, noise, fire safety, automatic protection systems. |
Implementation Timeline and Stages | Establishment of deadlines for the completion of individual stages of design and construction. | Work completion deadlines, coordination stages, equipment delivery schedule. |
Economic Indicators | Expected economic efficiency of the project, payback calculation. | Payback period, cost savings, expected profit. |
Preparation and Coordination of the ToR
Preparation of the technical specifications includes the following stages:
1. Collection of initial data — results of engineering surveys, data from pre-project surveys, customer requirements.
2. Formulation of equipment requirements — selection of optimal technical solutions based on the analysis of similar facilities.
3. Determination of operating modes — selection of parallel or autonomous (island) mode depending on the project goals.
4. Coordination with the customer — discussion and approval of all sections of the ToR, including power parameters, reliability, and cost requirements.
5. Approval of the ToR — official approval of the document, which will be the basis for further project work.
Approved ToR document includes:
- Technical characteristics of the equipment (electrical and thermal power, efficiency, type of fuel).
- Requirements for connection to external utility networks and communications.
- Operational parameters (temperature range, humidity level, permissible noise level).
- Requirements for safety and environmental friendliness (limitations on emissions, requirements for automatic protection systems).
- Economic indicators (payback calculation, planned cost savings).
- Work schedule (design, construction, and commissioning deadlines).
- Formalized document — this is an electronic format of an official document, formed in accordance with the approved format of the Federal Tax Service. It has a clearly structured form and content.
Example of ToR for a 1 MW mini CHP plant
Parameter | Description | Example Values |
Electrical Power (Pe) | Maximum electrical power of the CHP plant. | 1 MW ± 5% |
Thermal Power (Q) | Maximum thermal power required for heating or technological processes. | 1-2 MW (in cogeneration mode) |
Type of Fuel | Type of fuel used (natural gas, biogas, diesel fuel). | Natural gas, pressure 0.3-0.6 MPa |
Specific Cost of Fuel (Cfuel) | Price of fuel per unit of energy (RUB/m³, RUB/kg). | 4-5 RUB/m³ for natural gas |
Electrical Efficiency (ηe) | Efficiency for electricity generation. | 38-45% |
Overall Efficiency (ηo) | Efficiency considering the total generation of electricity and heat. | At least 85% |
Thermal Efficiency (ηt) | Efficiency for heat generation. | 40-50% |
Specific Fuel Consumption (B) | Amount of fuel required to generate 1 kW of electricity. | 0.2-0.25 m³/kW·h |
Enterprise Electricity Consumption | Average daily and maximum electricity consumption. | 0.8-1.2 MW |
Peak Loads | Maximum loads during certain periods of operation. | 1.2-1.5 MW |
Equipment Lifespan | Average lifespan of equipment before major overhaul. | At least 60,000 hours |
Operating Mode | Continuous or cyclic operation mode. | Continuous, 8000 hours per year |
Noise Level | Permissible noise level at a certain distance from the equipment. | No more than 85 dB at a distance of 1 m |
Operating Temperature Range | Range of temperatures at which the equipment can operate effectively. | From -40 to +40 °C |
Cooling System | Type of cooling system (air, liquid, hybrid). | Air or liquid cooling |
Emission Requirements | Permissible levels of pollutant emissions. | Compliance with MPE (maximum permissible emissions) standards |
Backup | Possibility of connection to external networks for emergency power supply. | Possibility of operation with an external source |
Commissioning Time | Time required to commission the equipment. | No more than 6 months from the date of project approval |
Economic Efficiency | Indicators of payback and profitability of the facility. | Payback period of no more than 3 years |
Guarantees | Period of trouble-free operation under operating conditions. | Minimum 2 years of trouble-free operation |
Environmental Conditions | Temperature, humidity, altitude above sea level. | -20°C to +30°C, altitude up to 200 m |
Backup Fuel | Alternative type of fuel in the absence of the main fuel. | Propane-butane, diesel fuel |
Mini CHP Plant Diagram
Used for the development and coordination of technical specifications, as well as for determining the layout of equipment and main technological units. The mini CHP plant diagram includes the following elements:
- Location of the main equipment (generators, engines, heat exchangers).
- Fuel supply and distribution schemes.
- Cooling and heat recovery systems.
- Routes of electrical cables and pipelines.
- Automation and control systems.
- Noise and vibration protection elements.
The diagram also takes into account operating modes (autonomous, parallel, island) and placement features (container, block-module, casing, water platform, etc.).
Selection of Operating Mode for Mini CHP Plant
During the design phase, at the stage of developing the technical specifications (ToR), it is necessary to select the operating mode for the mini CHP plant. There are two variants of the operating mode: parallel with the grid and autonomous (island mode).
Parallel operation with the grid — a mode in which the mini CHP plant is connected to the centralized power grid and can both consume and supply electricity to the grid.
Advantages of parallel operation mode of mini CHP plant with the grid:
- Possibility of selling excess electricity to the grid.
- Guarantee of uninterrupted power supply with the presence of an external network.
- More flexible power management and optimization of energy consumption.
Disadvantages:
- Dependence on the external power grid.
- Need for complex synchronization and equipment setup for stable operation.
- Requirements for the quality of electrical energy (frequency, voltage) in the grid.
Autonomous mode (island) — the mini CHP plant is completely independent of the external grid and provides energy to the enterprise locally. This mode is often used for facilities located far from centralized power grids or in cases where complete energy independence is required.
Advantages of autonomous operation mode of mini CHP plant:
- Complete energy independence.
- Ability to operate during external network outages.
- Increased reliability of power supply in conditions of unstable external networks.
Disadvantages:
- Need for power reserve to ensure reliability.
- More complex load and generation management.
- Requires additional measures to maintain frequency and voltage stability.
Types of Mini CHP Plant Structures
During the development of basic technical solutions (BTS), issues of structure, equipment layout, type of cooling, and other technical solutions are being worked out.
1. Containerized Mini CHP Plant
- Description: Compact power plant mounted in a metal container with thermal and noise insulation.
- Advantages: Quick installation, mobility, protection from weather conditions and vandalism.
- Disadvantages: Limited modernization capabilities, need for enhanced ventilation.
- Application: Construction sites, temporary energy facilities, remote facilities with limited infrastructure.
2. Modular Mini CHP Plant
- Description: Consists of separate blocks (modules) for main units: generator, cooling system, gas cleaning, etc.
- Advantages: Flexibility in design, possibility of power expansion, simplified transportation.
- Disadvantages: More complex on-site assembly, high requirements for the foundation.
- Application: Factories, large industrial facilities, CHP plants at facilities with variable load.
3. Mini CHP Plant in a Casing (Hooded Design)
- Description: Installation with an external metal casing for noise insulation and equipment protection.
- Advantages: High degree of noise insulation, compactness, protection from external influences.
- Disadvantages: More complex maintenance, limited access to equipment units.
- Application: Facilities in urban areas, buildings with high noise level requirements.
4. Floating (on water) Mini CHP Plant
- Description: Power plant located on a floating platform or barge.
- Advantages: Flexibility in placement, independence from land communications, high mobility.
- Disadvantages: High costs for construction and operation, complex technical maintenance.
- Application: Ports, coastal areas, remote island facilities.
5. Stationary (capital) Mini CHP Plant
- Description: Permanent installation integrated into a building or a specially constructed structure.
- Advantages: High reliability, long lifespan, possibility of scaling.
- Disadvantages: High construction cost, long installation periods.
- Application: Factories, large industrial enterprises, CHP plants as part of large energy complexes.
6. Noise-protected Mini CHP Plant with Screening
- Description: Power plant equipped with noise protection screens to minimize noise.
- Advantages: Effective local noise protection, compliance with sanitary standards.
- Disadvantages: Requires additional space for screen installation, increased costs.
- Application: Facilities in residential areas, hospitals, office centers.
7. Mobile Mini CHP Plant
- Description: Installation on a chassis or trailer for quick transportation.
- Advantages: High mobility, readiness for quick deployment, possibility of temporary use.
- Disadvantages: Limited power, need for frequent technical maintenance.
- Application: Emergency services, construction sites, temporary facilities.
8. Underground Mini CHP Plant
- Description: Installation located underground to minimize environmental impact and noise loads.
- Advantages: Maximum protection from external factors, absence of visual impact on the landscape.
- Disadvantages: High construction costs, complex maintenance.
- Application: Mining enterprises, military facilities, urban CHP plants.
9. Hybrid Mini CHP Plant
- Description: Installation combining several types of energy sources (gas, biogas, hydrogen).
- Advantages: Flexibility in fuel choice, high efficiency, possibility of reducing emissions.
- Disadvantages: High complexity of management, need for complex automation.
- Application: Energy-efficient complexes, projects with low carbon footprint requirements.
10. Mini CHP Plant with Heat Recovery
- Description: Station using excess heat for heating or technological processes.
- Advantages: High overall efficiency, reduction in heating costs, possibility of cogeneration.
- Disadvantages: Requires a complex heat exchange system, high capital costs.
- Application: Factories, greenhouse farms, facilities with high thermal loads.
11. Mini CHP Plant with Integrated Electrical Energy Storage Systems (EESS)
- Description: Installation with batteries or accumulators to smooth peak loads.
- Advantages: Stable power supply, possibility of autonomous operation, reduction in peak costs.
- Disadvantages: High cost of battery systems, complex charge management.
- Application: Facilities with variable load, energy-efficient complexes, island networks.
Noise Insulation of Mini CHP Plant
In modular and containerized mini CHP plants of the MKC Group of Companies, sandwich panels with noise-absorbing characteristics are used, providing a noise reduction of 31-32 dBA. Such panels consist of metal claddings and an inner layer of mineral wool, effectively absorbing sound waves.
Regulatory Requirements for Noise Level of Mini CHP Plant
When designing a mini CHP plant, noise impacts must be considered as they can affect the comfort of personnel work and compliance with sanitary standards. The main regulations governing the permissible noise level of a mini CHP plant:
- GOST 31295.2-2005 (ISO 9613-2:1996) — "Acoustics. Noise assessment on open spaces. Part 2. General method for calculating sound attenuation."
- SanPiN 1.2.3685-21 — sanitary standards for permissible noise levels at workplaces.
- GOST 12.1.003-83 — "Occupational Safety Standards System. Noise. General safety requirements."
These regulations set permissible noise levels for industrial facilities, considering their location and degree of impact on the environment.
Table of Permissible Noise Levels Depending on the Structure of the Mini CHP Plant
Mini CHP Plant Structure | Average Noise Level, dB(A) | Advantages | Disadvantages | Material and Principle of Operation |
Open Installation | 110-130 | Simplicity of installation and maintenance | High noise level, requires noise insulation | Metal frames, sound propagates freely |
In a Container | 85-95 | Partial noise insulation, protection from weather conditions | Requires additional vibration protection | Metal structure with internal noise insulation (mineral wool, acoustic panel) |
With Noise Protection Casing | 75-85 | Maximum noise insulation, compliance with sanitary standards | Higher cost, complexity of maintenance | Durable metal casings with multilayer insulation (steel, mineral wool, vibration isolation materials) |
Noise Protection Screens | 70-80 | Effective local noise protection | Requires space for installation, reduces overall accessibility of equipment | Panels made of perforated steel, aluminum, or composite materials, filled with sound-absorbing materials (acoustic wool, polyurethane foam) |
Fully Enclosed Room | 65-75 | Minimum noise level, protection from weather conditions | High cost of construction and operation | Reinforced concrete structures with multilayer sound insulation (concrete, aerated concrete, mineral wool) |
Principle of Operation of Noise Protection Screens
Noise protection screens are designed to block and absorb sound waves emanating from the mini CHP plant. They reduce the noise level by:
- Sound reflection — dense metal panels block the propagation of sound waves.
- Sound absorption — multilayer structure with porous materials effectively dampens sound vibrations.
- Diffusion — the surface of the panels can be perforated to reduce resonance and evenly distribute sound.
- Vibration reduction — use of materials with high viscosity, reducing the transmission of mechanical vibrations.
The table above shows the average noise levels measured inside or near the installation, which may vary depending on the specific configuration of the equipment, quality of installation, and additional noise insulation measures.
For a more accurate representation of information in the table, the following should be distinguished:
- Airborne sound insulation index Rw: characteristic of a material or structure showing by how many decibels the sound transmission through it is reduced.
- Actual noise level near the installation: depends on many factors, including equipment power, presence of additional noise protection measures, and operating conditions.
The technical specifications are not just a formal document, but the basis for all subsequent stages of design. Its quality directly affects the success of construction and operation of the mini CHP plant, as well as the economic efficiency of the project as a whole.
Result of the Technical Specifications Development Stage
The result of the technical specifications development stage is a formalized document that describes in detail all technical, operational, and economic requirements for the future facility and serves as the basis for further design and construction.
Formalized document — this is an electronic format of an official document, formed in accordance with the approved format of the Federal Tax Service. It has a clearly structured form and content.
4. Development of Project Documentation (PD)
At the stage of developing project documentation and working documentation, a complete set of documents necessary for the construction and further operation of the facility is prepared. The main task is to create detailed, technically correct, and coordinated materials that will serve as instructions for contractors and performers.
Project Documentation (PD) — this is a set of documents defining architectural, technical, technological, structural, and organizational solutions for the construction or reconstruction of a facility.
It includes the following main sections:
- General data and technical solutions: description of the facility, main technical characteristics, layout scheme, requirements for materials and equipment.
- Architectural solutions: plans and sections of the building, facades, spatial layout.
- Structural solutions: calculations and drawings of foundations, frameworks, walls, floors.
- Utility networks: schemes of power supply, heating, ventilation, water supply, and sewage.
- Technological part: description of the technological process, schemes of equipment installation, connection of communications.
- Measures for environmental protection and safety.
5. Development of Working Documentation (WD)
Working Documentation (WD) — these are detailed drawings, specifications, and instructions based on which construction and installation of equipment will be carried out. WD includes:
- Working drawings with exact dimensions, materials, units, and details.
- Specifications of equipment and materials that must be purchased and installed.
- Explanatory notes indicating the technology of work performance, quality requirements, and control methods.
- Estimates and schedules for construction and installation work.
Significance of the stage:
- Allows clearly defining the scope and sequence of work.
- Ensures the possibility of obtaining necessary approvals and permits.
- Serves as the basis for concluding contracts with contractors.
- Guarantees compliance with all technical and regulatory requirements.
- Minimizes the risks of errors and rework at the construction site.
Example for a 1 MW mini CHP plant:
- In the PD, the installation scheme of the gas piston engine, fuel supply, heat removal system, and flue gases, as well as the utility networks of the facility, will be described.
- The WD contains working drawings of the foundation for the equipment, plans for connection to the power grid and gas pipeline, specifications of cables and pipes.
- Explanatory notes will explain the features of the installation of the gas piston unit, taking into account safety and environmental protection requirements.
Result of the Development of PD and WD
The completed result of the stage "Development of Project Documentation (PD) and Working Documentation (WD)" is considered a fully prepared and coordinated set of documents, which includes:
- Project Documentation (PD) — a complete package of project solutions, including architectural, structural, technological, engineering, and organizational sections, formatted according to the requirements of regulatory acts and standards.
- Working Documentation (WD) — detailed working drawings, specifications of equipment and materials, explanatory notes, and estimates necessary for construction and installation work.
- Documents have passed internal checks and corrections.
- Project documentation is coordinated with the customer and approved in the prescribed manner.
- Documents are ready for submission to state expertise bodies (if required) to obtain construction permits.
- Documentation is transferred to contractors for construction and installation work.
Thus, the result of the stage is a complete, coordinated, approved, and ready-to-implement set of project and estimate documentation, which serves as the basis for further construction and commissioning of the facility.
6. Creation of Project and Estimate Documentation (PED)
The goal of the project and estimate documentation stage is to determine the exact cost of constructing a mini CHP plant, including all expenses for equipment, materials, installation and commissioning work, as well as subsequent technical maintenance. PED serves as the basis for financial planning and investment calculations.
Main Elements of PED:
1. Technical Part (PD and WD)
- Architectural drawings and structural schemes of buildings and facilities.
- Equipment layout plans.
- Utility network schemes (power supply, heat supply, gas supply, water supply).
- Automation and dispatching schemes.
- Plans for connection to existing infrastructure.
2. Estimate Part (ED)
- Calculation of the cost of main materials and equipment.
- Calculation of the cost of installation and construction work.
- Calculation of transportation and logistics costs.
- Accounting for unforeseen expenses and risk coefficients.
- Calculation of the cost of commissioning work and author supervision.
Main Calculations in Project and Estimate Documentation:
Determination of Mini CHP Plant Power
Pм = Qпотреб / ηэл
where:
Pм — power of the mini CHP plant, kW;
Qпотреб — required thermal power, kW;
ηэл — electrical efficiency of the equipment (usually 35-45%).
Calculation of Fuel Savings
Eтопл = (Pм × T × ηтепл) - Qпотреб
where:
Eтопл — fuel savings, kW;
T — number of operating hours per year;
ηтепл — thermal efficiency of the equipment (usually 40-50%).
Calculation of Capital Costs
Cкап = Cобор + Cмонтаж + Cстроит + Cпуск + Cлогист
where:
Cкап — total capital costs, RUB;
Cобор — cost of main equipment;
Cмонтаж — cost of installation work;
Cстроит — cost of construction work;
Cпуск — cost of commissioning work;
Cлогист — cost of equipment transportation.
Table of Approximate Costs for Main Components of a 2 MW Mini CHP Plant:
Name | Quantity | Cost per Unit, RUB | Total Cost, RUB |
Gas Piston Unit | 2 units | 30,000,000 | 60,000,000 |
Gas Supply System | 1 set | 8,000,000 | 8,000,000 |
Heat Exchanger System | 1 set | 6,000,000 | 6,000,000 |
Electric Generator | 2 units | 12,000,000 | 24,000,000 |
Automation System | 1 set | 5,000,000 | 5,000,000 |
Installation Work | 15,000,000 | ||
Construction Work | 20,000,000 | ||
Commissioning Work | 5,000,000 | ||
Transportation | 2,000,000 | ||
TOTAL: | 145,000,000 |
Estimation of Operating Costs (OPEX)
OPEX = Cтопливо + Cобслуж + Cамортизация + Cперсонал
where:
Cтопливо — fuel costs;
Cобслуж — maintenance costs;
Cамортизация — depreciation of main equipment;
Cперсонал — personnel costs.
Example of Calculation of Annual Fuel Costs for a 2 MW Mini CHP Plant:
- Average consumption of natural gas — 0.2 m³/kW·h
- Price of natural gas — 7 RUB/m³
- Number of operating hours per year — 8000 h
Cтопливо = Pм × 0.2 m³/kW·h × 8000 h × 7 RUB/m³ = 22,400,000 RUB
Final Calculation of Capital and Operating Costs:
CAPEX + OPEX = 145,000,000 + 22,400,000 = 167,400,000 RUB/year
PED also includes a construction schedule, financial model of the project, payback calculations (NPV, IRR), feasibility study (FS), and risk analysis.
Feasibility Study (FS)
Feasibility Study (FS) — this is a document that evaluates the technical and economic feasibility of constructing a mini CHP plant. It includes a detailed analysis of project solutions, cost calculations, and forecast of the financial efficiency of the project.
Goals of FS:
- Evaluation of the overall economic efficiency of constructing a mini CHP plant.
- Confirmation of the commercial viability of the project.
- Reduction of investment risks through more accurate forecasting of costs and revenues.
- Determination of optimal technical solutions for maximum efficiency of the facility.
Main Sections of FS:
1. Technical Part:
- Description of the designed equipment (gas piston units, heat exchangers, generators).
- Analysis of available technologies and their efficiency.
- Technical calculations (performance, efficiency, reliability).
2. Economic Part:
- Evaluation of capital costs (CAPEX) and operating costs (OPEX).
- Calculation of payback, net present value (NPV), and internal rate of return (IRR).
- Forecast of revenue and costs for the entire lifespan of the mini CHP plant.
3. Risk Analysis:
- Evaluation of technological, financial, and environmental risks.
- Measures to reduce risks (insurance, reserve capacities, contractual guarantees).
Formulas and Calculations:
Net Present Value (NPV):
NPV = Σ (Ct - OPEXt - CAPEXt) / (1 + r)^t - I0
where:
Ct — cash flows in year t;
OPEXt — operating expenses in year t;
CAPEXt — capital costs in year t;
r — discount rate;
I0 — initial investments.
Internal Rate of Return (IRR):
Σ (Ct - OPEXt - CAPEXt) / (1 + IRR)^t = I0
Advantages of Developing FS:
- Reduction of investment risks.
- Accurate assessment of the project's payback period.
- Increased chances of obtaining financing and benefits.
- Determination of the optimal financing structure.
Example of NPV Calculation for a 2 MW Mini CHP Plant:
Suppose the annual revenue from selling electricity is 40 million RUB, operating expenses are 20 million RUB, and capital costs are 145 million RUB. The discount rate is 12%, and the operating life is 10 years.
NPV = Σ (40 - 20) / (1 + 0.12)^t - 145 = 51.4 million RUB
Result:
A positive NPV value confirms the economic feasibility of constructing the mini CHP plant, making the project attractive for investors and customers.
7. Customer Support During State Expertise
State expertise of project documentation and results of engineering surveys is a mandatory procedure provided by Federal Law No. 190-FZ "Urban Planning Code of the Russian Federation" and Government Decree No. 145 dated 05.03.2007. The purpose of the expertise is to check the compliance of project solutions with safety requirements, economic efficiency, energy efficiency, and environmental protection.
Main Tasks at the Support Stage:
1. Checking the Completeness and Compliance of Documentation:
- Completeness of project documentation (PD), working documentation (WD), technical specifications (TS), and project and estimate documentation (PED).
- Compliance of technical solutions with the requirements of SP (Codes of Practice), GOST, and SNiP.
- Verification of calculations of strength, stability, heat losses, and energy efficiency.
2. Adjusting the Project Based on Experts' Comments:
- Elimination of identified inconsistencies.
- Recalculation of technical indicators if necessary.
- Preparation of explanatory notes and additional justifications.
3. Preparation of Justifications for Disputed Issues:
- Economic justification of the feasibility of selected solutions.
- Documents confirming the safety of structures and units.
- Feasibility study (FS) of the facility's capacity:
E = P × T / η
where:
- E — annual energy consumption, kW·h,
- P — installed electrical capacity of the mini CHP plant, kW,
- T — annual time of use of installed capacity, hours,
- η — efficiency (coefficient of performance) of the system.
Calculation of Energy Efficiency:
To justify the energy efficiency of the project, the formula for calculating annual savings is used:
ΔE = (Cэл - Cгаз) × E
where:
- ΔE — savings per unit of energy, RUB/year,
- Cэл — average cost of purchased electricity, RUB/kW·h,
- Cгаз — specific cost of electricity generated by the mini CHP plant, RUB/kW·h.
Example of Calculation:
Suppose the capacity of the mini CHP plant is 2000 kW, annual load is 6000 hours, efficiency is 85%, cost of purchased electricity is 9 RUB/kW·h, cost of electricity from the mini CHP plant is 4 RUB/kW·h:
E = 2000 × 6000 / 0.85 = 14.1 million kW·h/year
ΔE = (9 - 4) × 14.1 = 70.5 million RUB/year
Formatting Tables and Calculations:
Parameter | Value | Unit of Measurement |
Capacity | 2000 | kW |
Load | 6000 | hours |
Efficiency | 85 | % |
Cost of Purchased Electricity | 9 | RUB/kW·h |
Cost of Electricity from Mini CHP Plant | 4 | RUB/kW·h |
Savings | 70.5 | million RUB/year |
Result of the Stage:
- Positive conclusion of the state expertise.
- Confirmation of compliance of project solutions with safety, energy efficiency, and environmental requirements.
- Final coordination of the project and readiness for the construction stage.
After obtaining a positive conclusion from the state expertise and formalizing the permitting documentation, one can proceed to the construction stages. The stages of author supervision and technical supervision are control stages that take place during construction to verify compliance of the completed work with the project documentation and regulatory requirements.
- Author Supervision: control of compliance of construction with the project solutions specified in the documentation.
- Technical Supervision: control of quality, safety, and compliance with technical regulations and standards at the construction site.
They ensure that the constructed facility fully complies with the approved project and standards.
8. Author Supervision
Author supervision — is a systematic control over the progress of construction and installation work of the mini CHP plant, aimed at ensuring full compliance of the completed work with the approved project documentation and technical requirements.
Main Tasks and Activities of Author Supervision:
- Regular inspections of the construction site, equipment, and installation work by specialists involved in the project development.
- Quality control of materials used and compliance with technological processes.
- Identification and prompt elimination of identified deviations, errors, and shortcomings that may affect the reliability and safety of the mini CHP plant operation.
- Interaction with contracting organizations and the customer to coordinate necessary changes and adjustments to the project in case of non-standard situations.
- Preparation of control acts and reports on conducted inspections for documentary confirmation of compliance of the completed work with the project documentation.
- Participation in the acceptance of individual stages and final acceptance of the facility.
The result of the author supervision stage is considered to be:
- Confirmation of compliance of the completed construction and installation work with the project documentation.
- Absence of significant comments and defects affecting the operation of the mini CHP plant.
- Availability of executed control acts and reports confirming the quality of the completed work.
- Reduction of risks of emergency situations and increased reliability of the facility operation.
- Signing of the final act of author supervision, which testifies to the fulfillment of all requirements and readiness of the facility for further operation.
Thus, the author supervision stage ensures the reliability, safety, and quality of the constructed mini CHP plant, minimizing possible technical risks and guaranteeing compliance with project solutions.
9. Technical Supervision
Technical supervision — is the control over the compliance of construction and installation work with project documentation, requirements of technical regulations, SNiP, SP, and GOST. This stage is carried out to ensure the quality of construction, reliability, and safety of facilities such as mini CHP plants.
Main Tasks of Technical Supervision:
1. Checking the compliance of construction work with project documentation:
- Quality control of installation work.
- Verification of compliance with technical solutions embedded in the project.
- Accounting for actual volumes of work and materials used.
2. Quality control of materials used:
- Verification of passports, certificates of conformity, and declarations of conformity.
- Quality control of welded joints, concrete, metal structures, and other construction materials.
- Testing and laboratory research of material samples.
3. Technical control of installation of engineering systems:
- Verification of pipeline tightness (hydraulic tests).
- Testing of electrical networks and devices for compliance with the parameters of project documentation.
- Control of thermal insulation parameters, anti-corrosion protection, and vibration isolation.
4. Documentation of results:
- Compilation of acts of inspection of hidden work.
- Maintenance of technical supervision journals.
- Execution of as-built drawings, verification, and correction of working documentation.
Formulas and Calculations for Compliance Control:
To verify the quality of welded joints, the formula for calculating the strength of a welded joint is used:
σ = F / A
where:
σ — stress in the welded joint, MPa,
F — force acting on the joint, N,
A — cross-sectional area of the joint, mm².
Example:
If the force F = 5000 N, and the joint area A = 50 mm², then:
σ = 5000 / 50 = 100 MPa
This result should be less than the allowable stress for this material, for example, for steel grade 09G2S (σd = 350 MPa).
Hydraulic Tests of Pipelines:
Pt = Pr × k
where:
Pt — test pressure, MPa,
Pr — operating pressure, MPa,
k — safety factor (usually 1.5 for steel pipes).
Example:
For a system with an operating pressure of 1.6 MPa:
Pt = 1.6 × 1.5 = 2.4 MPa
Documentation:
Document | Description |
Technical Supervision Journal | Record of all inspections and comments on the quality of work |
Act of Inspection of Hidden Work | Confirmation of the quality of completed hidden structures |
As-Built Drawings | Documentation of the actual placement of engineering networks |
Result of the Stage:
- Confirmation of compliance of the completed work with the project documentation.
- Identification and elimination of defects at the construction stage.
- Preparation of the construction facility for commissioning.
Differences Between Author and Technical Supervision
Parameter | Author Supervision | Technical Supervision |
Main Goal | Ensuring compliance of construction solutions with project documentation | Control of quality and safety of construction and installation work |
Performers | Project organization or authors of project documentation | Specialized engineers or customer's technical control services |
Documents for Control | Project Documentation (PD), Working Documentation (WD) | Technical regulations, SNiP, SP, GOST, as-built drawings |
Main Tasks | Verification of compliance of architectural, structural, and engineering solutions with the project | Verification of quality of materials, compliance of completed work with standards, control of technological processes |
Control Methods | Visual inspection, analysis of drawings, coordination of changes | Laboratory tests, instrumental measurements, acts of inspection of hidden work |
Documentation | Conclusion on compliance of construction with project solutions | Technical supervision journals, acts of inspection of hidden work, test protocols |
Result | Confirmation of compliance with project documentation | Confirmation of quality and safety of construction and installation work |
Responsibility | For the correctness of project solutions | For compliance of completed work with regulatory requirements |
Frequency of Control | Episodic, at key stages of construction | Continuous, at all stages of construction |
Preparation of Documentation | Preparation of changes and corrections to project documentation | Preparation of as-built documentation, verification of acts of completed work |
Conclusion
All stages of designing a mini CHP plant ensure the reliability, efficiency, and safety of the installation, minimize risks, and optimize costs. Each step requires a professional approach to meet technical and regulatory requirements, which ultimately guarantees the successful implementation of the project and its long-term efficient operation.
© MKC Group of Companies LLC, 2025