Repair of the GPU
Table of contents
Gas piston units (GPU) are a key element of power systems, providing generation of electric and thermal energy. Reliable operation of gas piston units directly affects the efficiency of the power system of the enterprise. However, like any technical equipment, gas piston units can encounter various faults that require prompt repair of the GPU engine. In this material we will consider in detail planned service actions and possible malfunctions of MWM GPU.
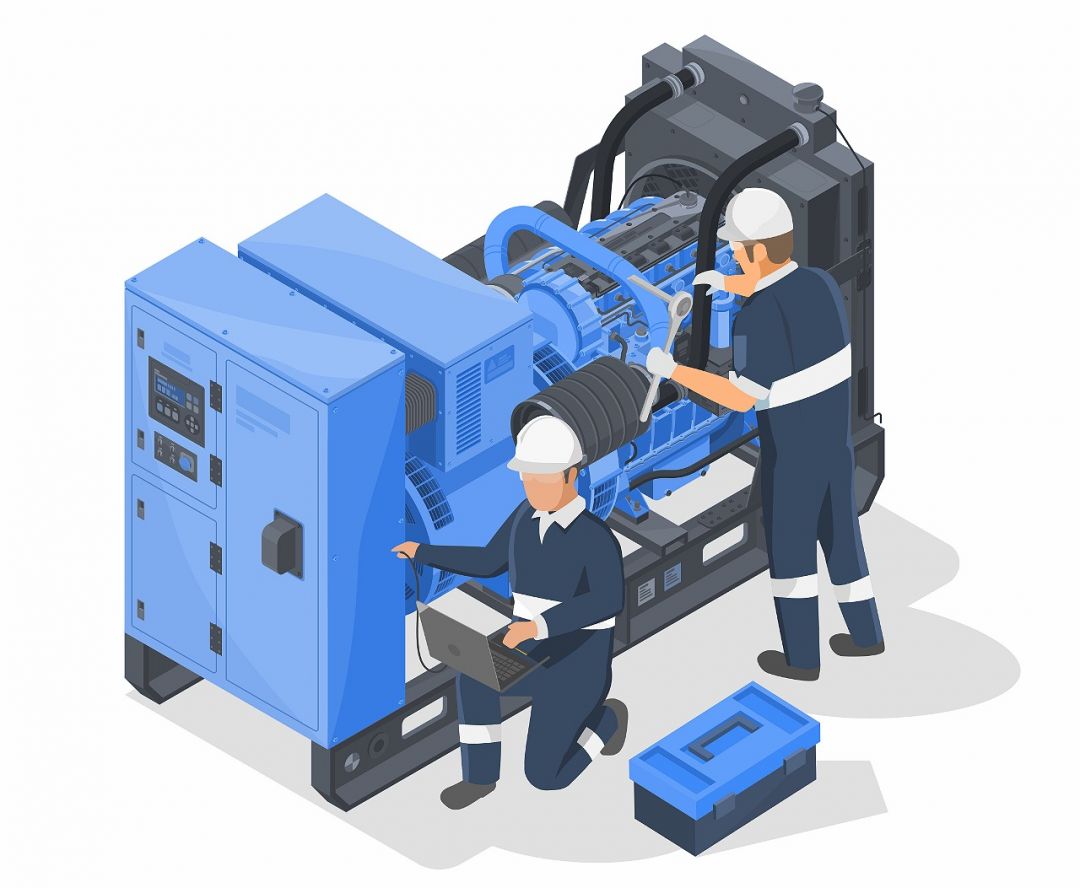
Classification of repairs of MWM gas piston units
Maintenance and repair activities are categorized into several types depending on the operating condition of the unit and the mileage (operating hours):
- E-10 to E-40: diagnostic inspections and checks. During these stages, the condition of the main components of the GPU is checked to identify potential defects or wear. During maintenance
- E40: according to MWM regulations oil and air filters are supposed to be replaced, spark plugs are replaced if necessary. At 8000 mth the crankcase gas filters are replaced.
- E-50 - E-60: medium repair. Within the framework of this repair, worn assemblies and parts are replaced, ignition and fuel supply systems are adjusted.
- E-70: major repair. This is the deepest and most complex type of repair, involving a complete disassembly of the unit, replacement of the main parts and assemblies, as well as restoring the performance characteristics of the engine.
These categories determine the nature of the work and help plan maintenance to ensure smooth operation of the units.
GPU repair stages
The repair process of a gas piston unit includes several stages:
- Fault diagnosis. The initial stage consists in identifying problematic components of the unit, using specialized diagnostic equipment, and checking the engine performance indicators.
- Determination of the causes of the malfunction. After the detection of defects, the causes of their occurrence are analyzed. This can be due to both wear and tear of parts and operational errors.
- Restoration of performance. At this stage, damaged assemblies and parts are replaced or repaired, fuel supply, ignition, cooling and other critical systems of the GPU are adjusted.
- Testing after repair. After repair, all operating parameters of the unit are checked to make sure that the equipment is reliable and working correctly.
Causes of gas piston unit (GPU) malfunctions
Gas piston units are subject to various types of malfunctions, which can be caused by both component wear and tear and external factors such as operating conditions, fuel quality and others. The following are the most common malfunctions of gas turbine units and possible causes of their occurrence:
Component |
Gas supply interrupted |
Possible causes |
The engine won't start |
Gas supply interrupted |
Gas shut-off elements closed, leakage, gas pressure regulator jammed |
|
Leakage |
|
|
Gas pressure regulator is stuck | |
|
Gas supply disrupted |
Gas pressure too high or too low |
|
Speed control is not possible |
Malfunction of the actuator |
|
Power supply interrupted |
Power supply to switch cabinet interrupted |
|
Cable breakage | |
|
The camshaft speed sensor does not give a signal |
Distance too far away |
Sensor or sensor cable defective | ||
Engine shut down by TEM system (cooling system not running) | Lack of coolant | |
Leakage |
||
Coolant pump defective | ||
Coolant pump leaks | ||
The cooling system is contaminated | ||
The engine won't start |
Gas supply interrupted |
Gas shut-off elements closed |
Power supply interrupted | The power supply to the machine switch cabinet has been interrupted. | |
Power supply to the starter has been interrupted | ||
Ignition does not work |
Spark plug defective | |
Ignition wire defective | ||
Ignition coil defective | ||
Ignition control unit defective | ||
Engine does not turn |
The starter system is defective | |
The camshaft frequency sensor does not give a signal |
Distance too far away | |
Flywheel frequency sensor does not signal | Too much distance | |
Ignition skipping and irregular engine running |
Gas supply interrupted |
Gas shut-off elements closed |
Power supply interrupted | The power supply to the machine switch cabinet has been interrupted. | |
Power supply to the starter has been interrupted | ||
Ignition does not work |
Spark plug defective |
|
Ignition wire defective |
||
Ignition coil defective | ||
Ignition control unit defective | ||
The motor does not turn |
The starter system is defective |
|
The camshaft speed sensor does not give a signal |
Too much distance |
|
The flywheel frequency sensor does not give a signal |
Distance is too great | |
The engine is overheating | Gas supply interrupted |
Gas shut-off elements closed |
Power supply interrupted |
Power supply to the machine switch cabinet has been interrupted | |
The starter power supply has been interrupted | ||
Ignition does not work |
Spark plug defective | |
Ignition wire defective | ||
Ignition coil defective | ||
Ignition control unit defective | ||
Engine does not turn
|
The starter system is defective | |
The camshaft speed sensor does not give a signal | Too far away | |
Flywheel speed sensor does not signal too far away | Too much distance | |
Engine ignition is irregular |
The ignition doesn't work |
Spark plug defective |
Ignition wire defective |
||
Ignition coil defective | ||
Ignition control unit defective | ||
Camshaft speed sensor signal too weak |
Too much distance | |
Frequency sensor defective | ||
Flywheel frequency sensor signal too weak | Too much distance | |
Frequency sensor defective | ||
The engine is overheating |
Insufficient heat transfer (between primary and secondary heating circuit) |
The heat exchanger is dirty |
Insufficient heat transfer (secondary heating circuit) |
3 way valve defective | |
Insufficient cooling capacity (cooling circuit) | Coolant pressure too low | |
Leakage |
||
Coolant pump defective |
||
The coolant pump is not sealing properly | ||
Table of exhaust system and supercharger faults |
Leaky flange connection on the exhaust gas heat exchanger | Defective gasket |
Loose threaded connection |
||
Insufficient capacity of the exhaust gas heat exchanger (pressure drop) | Water side contamination of the exhaust gas heat exchanger | |
Contamination of the OH heat exchanger on the side of the OH unit |
||
Water leakage at the condensate connection of the exhaust gas heat exchanger when the unit is switched off | Pressure vessel leaks | |
Threaded connection loosened | ||
Leaky flange connections of the suction air pipe |
Defective gasket | |
Threaded connection loosened | ||
Cooling system fault table |
Coolant pump does not work | Faulty fuse |
Cable clamp is loose | ||
Coolant pump defective | ||
Coolant pump performance is too low |
Air in the cooling system | |
Coolant pump connected in wrong direction of rotation | ||
Rotation speed is too low | ||
Coolant pump defective | ||
Coolant pump makes noises |
Initial pressure too low | |
Bearing malfunction | ||
Engine shut down by TEM system (lack of coolant) | Lack of coolant | |
Leakage | ||
Engine shut down by TEM (coolant temperature too high) | Lack of coolant | |
Coolant temperature sensor malfunction | ||
Table of pneumatic system faults |
Pneumatic starter does not respond | Empty compressed air tank |
Valves closed | ||
Insufficient compressed air |
||
Compressed air lines clogged |
||
Compressed air lines are leaking Compressed air lines are leaking |
||
Pneumatic starter malfunction | ||
Pneumatic starter does not reach the required speed |
Insufficient amount of compressed air | |
Compressed air lines are clogged | ||
Pneumatic starter rotates without thrust | Compressed air lines clogged | |
Pneumatic starter malfunction | ||
Table of coupling faults | Cracks in elastomer | Overloading of the coupling |
Coupling aging |
||
Coupling is incorrectly positioned |
||
Elastomer is detaching |
The coupling is not correctly positioned | |
Generator fault table |
Alternator voltage too high | Incorrect nominal value set |
Incorrect measurement lines connected | ||
Voltage regulator defective | ||
Alternator voltage fluctuations |
Inconsistent engine speed | |
Incorrect nominal value set | ||
Voltage regulator defective | ||
Generator voltage cannot be increased |
Setpoint adjuster or connection cable broken | |
Generator does not produce voltage | Excitation fuse blown | |
Exciter diodes defective | ||
Generator voltage drops significantly under load |
Drive speed decreases under load | |
Protective fuse defective | ||
Exciter diodes defective |
Benefits of regular maintenance
Regular maintenance of gas piston units not only helps reduce malfunctions, but also extends equipment life, reduces operating costs and improves overall plant efficiency. Maintenance recommendations include routine replacement of filters, oil and other consumables, as well as periodic inspection of systems for leaks, defects and wear.
Advantages of repair from “MKS”
- Original spare parts. Repair of gas piston units is carried out using only original spare parts. “MKS” has an operative stock of original spare parts and components supplied from manufacturing plants.
- Qualified specialists. Repair of gas piston plants of various brands and other equipment is performed by experienced engineers who have passed certified training at the manufacturing plants. The whole staff of the MKS service department is constantly improving its qualification and undergoing technical training.
- Minimal repair time. The extensive network of MKS branches in Russia ensures the presence of experienced specialists in different regions of the country. Together with the availability of spare parts and components that do not require additional delivery and customs clearance, this minimizes the time of GPU repair.
- Original service tools. MKS has at its disposal special service and repair kits designed for each type of engine. Repair of plants using other tools is inadmissible, as it leads to equipment breakdown.
Emergency repairs of gas turbine units
We also carry out emergency repairs of gas piston units, which may be required if the equipment is operated incorrectly. The main causes of accidents include unqualified maintenance, use of non-original spare parts and ignoring warnings about incorrect operation of the unit. The MKS team offers prompt specialist visit, diagnostics, estimation of the scope and cost of work, as well as supply of spare parts for necessary repairs.
Conclusion
Repair and maintenance of gas piston units play a key role in ensuring their reliable and long-term operation. It is important to follow a schedule of diagnostic inspections and scheduled repairs, such as E-10 through E-70, to keep your equipment in good working order and avoid costly downtime.
© MKC Group of Companies LLC, 2024