Trigeneration. What is it?
Table of contents
Tri+ Generation - Generating three types of energy at the same time: electricity, heat and cooling.
Trigeneration is a process in which part of the thermal energy produced by the operation of a reciprocating gas engine is used to produce refrigeration for the technological needs of the plant and for air conditioning.
Trigeneration working principle
The gas piston engine is supplied with fuel gas of the required parameters. The combustion of the fuel produces mechanical energy which is transmitted to the generator via a single shaft and converted into electrical energy with standard quality parameters.
When an internal combustion engine is running, a large amount of heat is released, which can be captured and used with the help of special equipment. At the same time, no additional fuel is used to produce this energy - it is a by-product of the technological process of generating electricity.
The system of heat utilisation from gas piston units allows to obtain thermal energy of the required parameters by means of heat exchangers and heat recovery boilers, by means of which heat is extracted from heated parts and media. The generated heat energy is supplied to the existing heat supply system of the company (cogeneration).
In addition to cogeneration, the simultaneous production of two energy resources, the gas piston plant can be used with specially installed equipment to organise trigeneration, the simultaneous production of three energy resources - electricity, heat and cold.
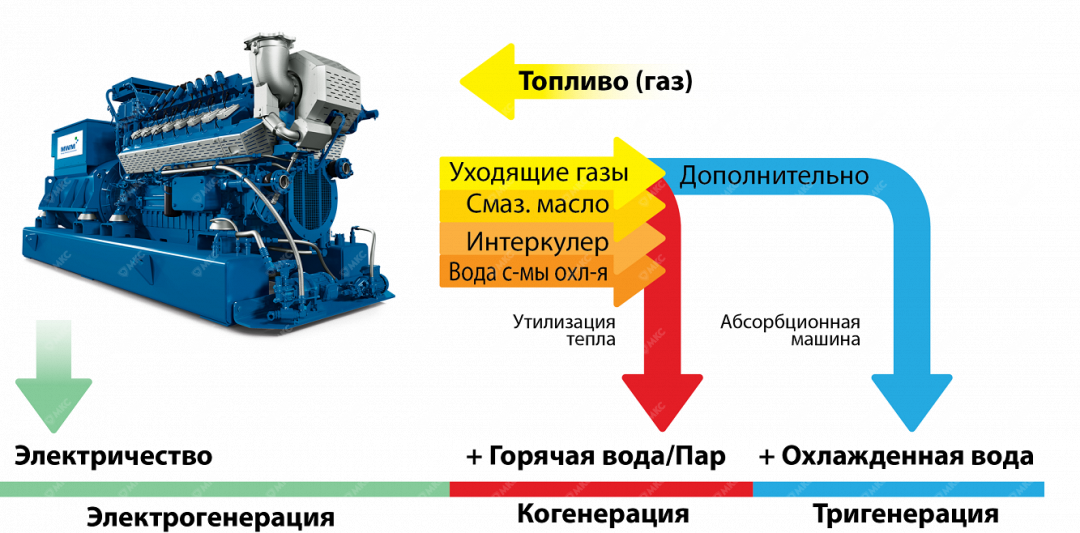
Trigeneration Scheme
Technologically, the trigeneration scheme is a connection of a gas piston plant with an absorption refrigeration machine.
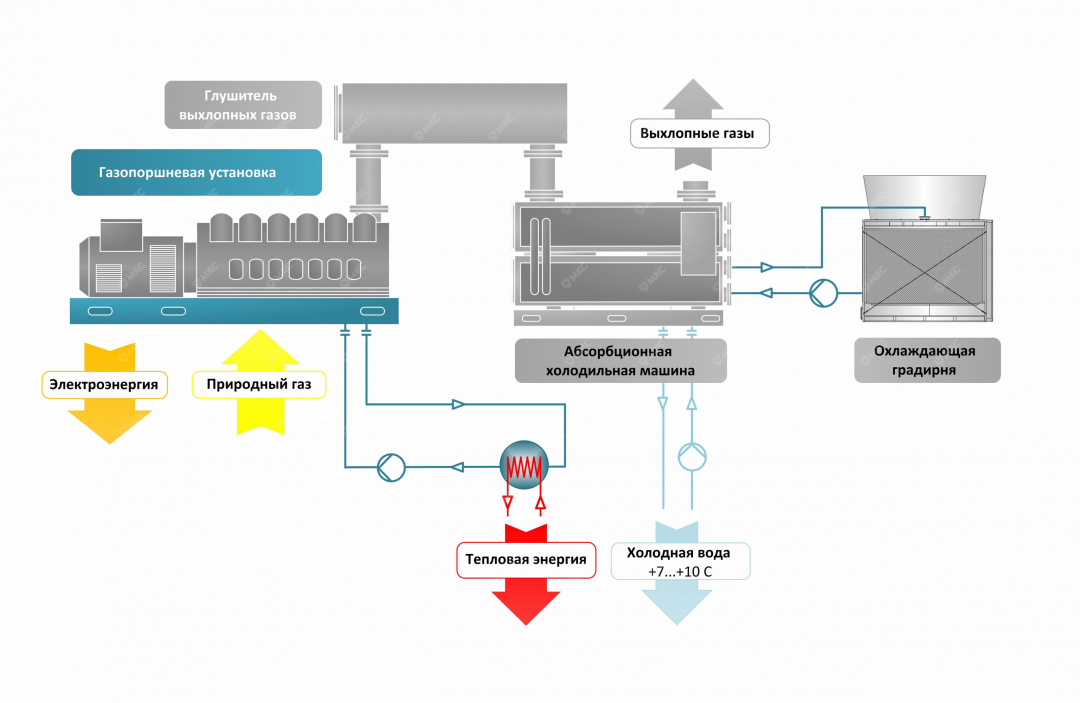
For trigeneration purposes, absorption lithium bromide refrigeration units (ABHM) are used - designed for extraction and removal of excess heat from thermal units and maintenance of specified optimal temperature and thermal regimes. Various solutions are used as an absorbent in them. Part of the heat recovered from the thermal units is fed to the ABHM to generate cold. The cold can be used both for water cooling and air conditioning systems, or for technological needs.
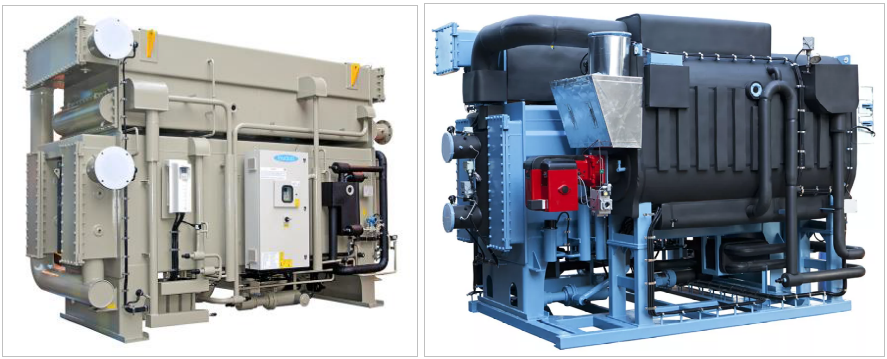
The ABHM is heated by hot water or steam. The process can take place in one or two stages. In a one-stage scheme, 600 kW of cold is produced from 1 MW of electrical energy, in a two-stage scheme - 1200 kW of cold.
ABHMs can be operated in two modes: cold and heat generation. Adsorption chillers operating in adsorption/desorption cycles and allowing to utilize thermal energy of not very hot water (80°C - 50°C) are in a special line. This is relevant in southern regions, where cooling needs are higher and electrical power is scarce, especially during peak demand periods.
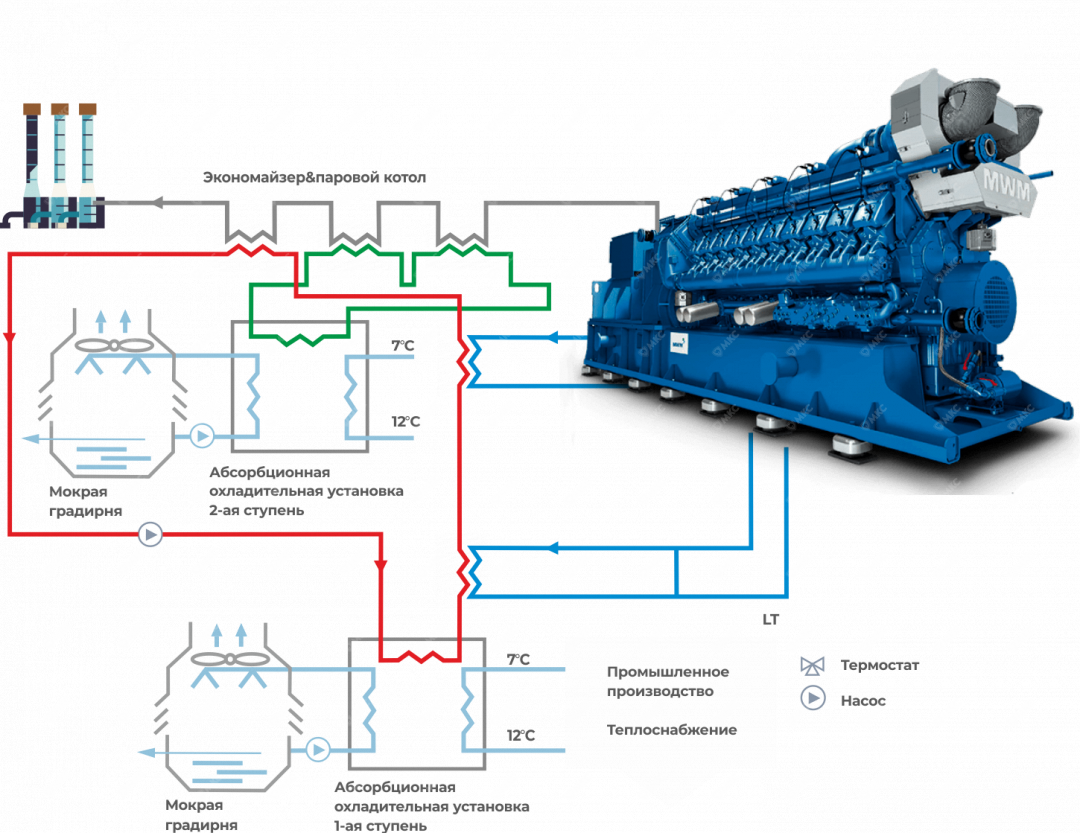
Applications
Trigeneration is used in various facilities where there is a need for electricity, heat and cold:
industrial enterprises;
agriculture;
service sector;
hotels;
trade and administrative centers;
business centers;
hospitals, health resorts and medical institutions;
pools, sports centers;
housing facilities;
airports;
refrigerated warehouses;
food storage bases;
In a number of applications utilized heat is used in low-temperature production processes, such as drying, tanning, food processing, heating of premises and water heating in buildings, cooling of premises with the help of absorption refrigeration machines.
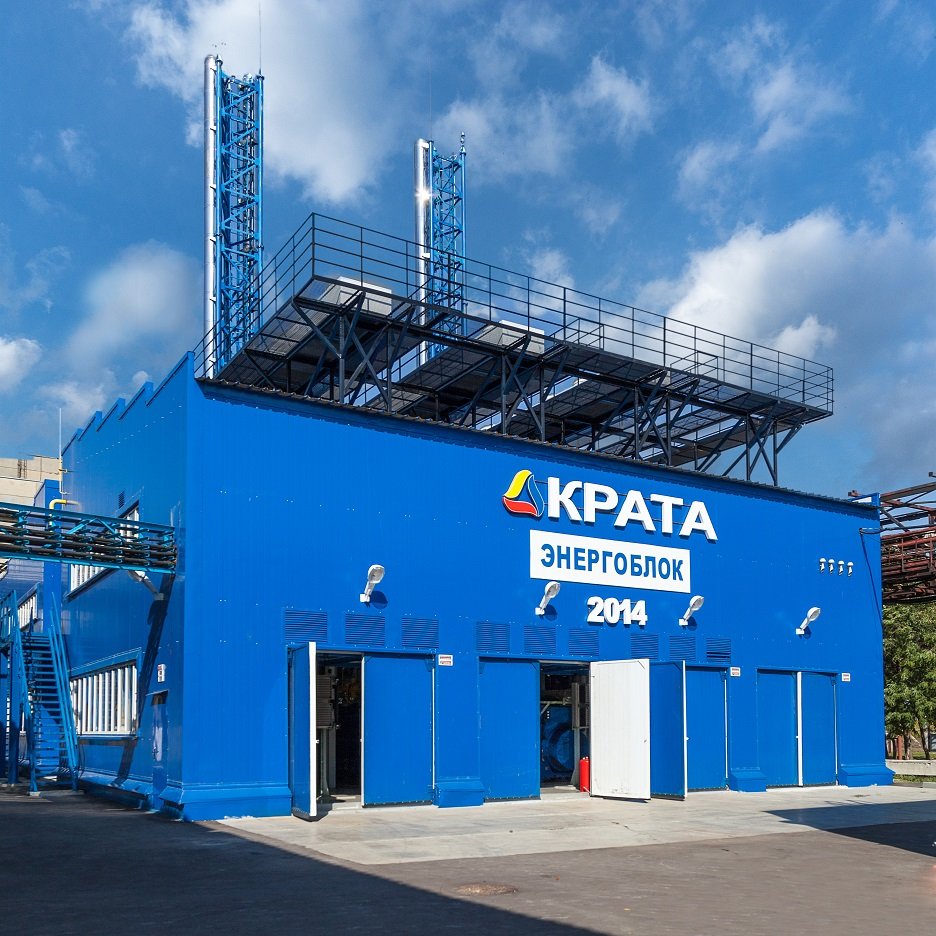
Advantages of trigeneration
Trigeneration plants are very profitable equipment in the field of small-scale distributed generation, as they allow the heat utilized from gas piston plants to be used not only in winter for heating purposes, but also in summer for space conditioning or cooling in technological needs. This increases the overall efficiency of the plant, which in such conditions can be used all year round while maintaining high efficiency.
Trigeneration projects have a number of advantages. The main ones are as follows:
Cost-effectiveness: surplus heat energy is used to produce cold, which has the lowest production cost
Addition of trigeneration cycle to the cogeneration plant increases the utilization factor of the unit throughout the year, which reduces its payback period and increases the efficiency of the invested investments
The operation of ABHM is almost twice cheaper than the operation of compression refrigeration machines
Absorption system works almost silently. Noise level at Q0 1500 kW does not exceed 65 dBa at a distance of 1 meter
Longevity: due to the absence of moving parts in the refrigeration unit and their wear and tear ABHM has an increased working life before overhaul - 20 years
ABHMs meet the requirements of international protocols for the protection of the ozone layer of the atmosphere, as no refrigerants are used in the absorption machines
Examples of realization
In 2014, a trigeneration energy complex for Pulkovo Airport was commissioned in St. Petersburg. The total cooling capacity of the energy center is 19 MW.
The trigeneration power complex provides the airport terminals with electricity, thermal energy (DHW, heating, ventilation) and cold for the needs of the air conditioning system.
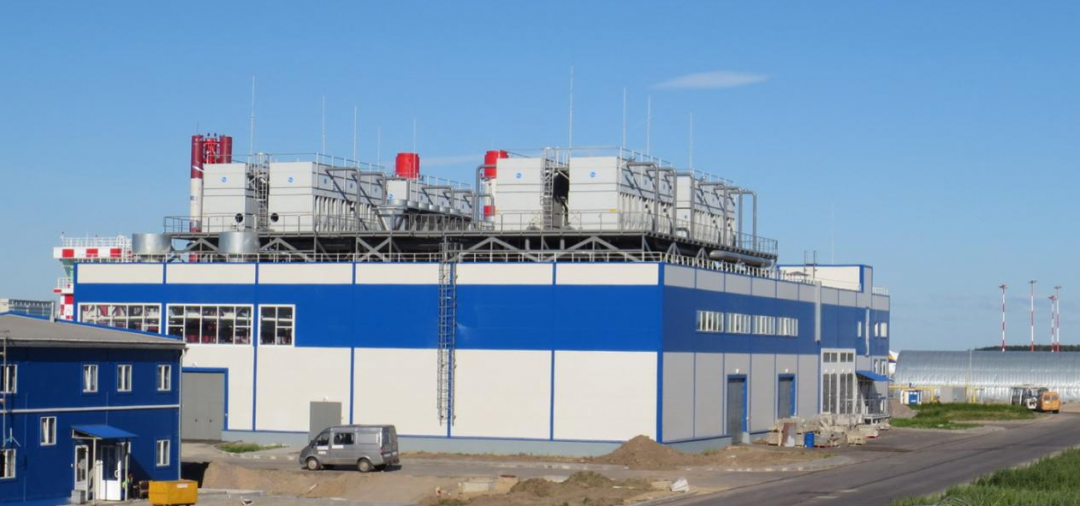
In 2015, MKS Group completed the construction of a mini-HPP for the largest enterprise of the Russian chemical industry, JSC Pigment.
The power center operates in the trigeneration mode. Three MWM TCG 2020 V20 gas piston units were used as the main generating equipment. Natural gas is used as fuel. The power center operates in parallel mode with the external grid.
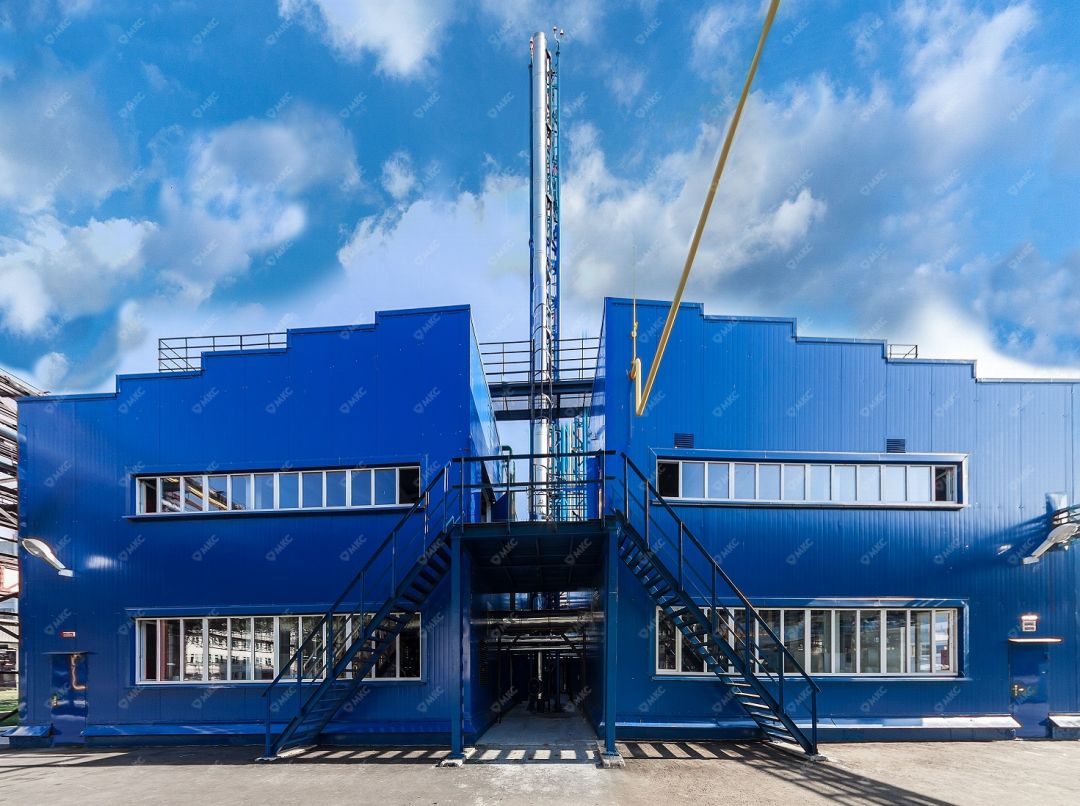
Trigeneration made it possible to efficiently use the utilized heat not only in winter for heating, but also in summer for air conditioning and for the technological needs of the enterprise. This approach made it possible to use the gas piston plant all year round, thereby not reducing its high efficiency in summer, when the need for generated heat decreases.
Thanks to trigeneration, the Pigment plant has reached a new level of energy efficiency. Energy savings became significant: the price of electricity decreased three times with the launch of the new plant, and heat and cold, as a by-product, became free of charge. The payback period of the facility was only 3 years.
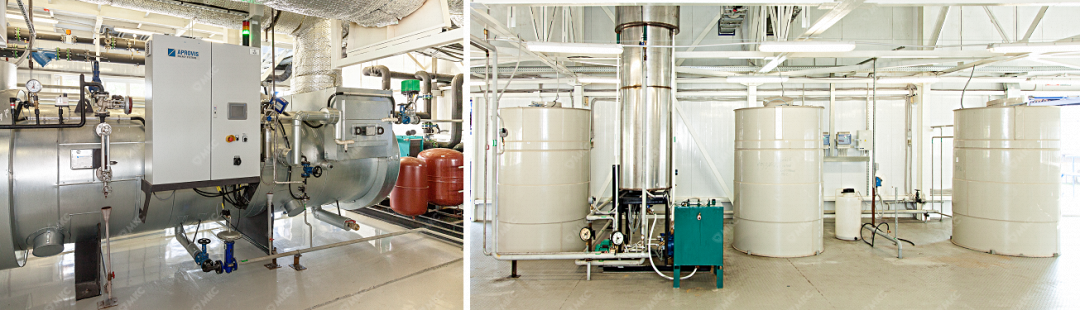
Economy and efficiency of trigeneration
Trigeneration plants increase efficiency for the consumer company in terms of its energy supply system. The main economic effect when using a trigeneration plant consists in obtaining associated conditionally free energy resources (heat, cold) without additional fuel costs. This effect leads to a noticeable reduction in the cost of electricity generation in relation to the monogeneration mode (only electricity generation), when all costs are allocated to only one resource. As a result of trigeneration, the consumer receives all generated resources much cheaper than from centralized networks.
Also, a significant criterion for trigeneration is the location of the generating facility in close proximity to the consumer - this reduces transmission losses and eliminates the transportation component in the cost of energy resources.
In this connection, projects of realization of gas-piston trigeneration power plants now have quite attractive payback period for the enterprise-consumer - up to 5 years. At the same time, the implementation period of such projects is usually within one calendar year, which makes trigeneration plant projects not only affordable, but also an obviously profitable and logical step.
Cost of implementation of trigeneration projects
The issue of cost of trigeneration projects implementation always remains one of the main issues. According to average estimates of engineering companies organizing the implementation of mini-HPP projects, the approximate unit cost of turnkey construction of such a facility in the cogeneration mode is about 650 euros per 1 kW of installed electric capacity. If the project is complicated up to the trigeneration mode, the preliminary unit cost can be up to 750-800 euros per 1 kW of installed electric capacity and higher, depending on the complexity and volume of equipment.
MKS Group is a leading engineering company in Russia, the main activity of which is the construction of small-scale power generation facilities - turnkey gas piston power plants. For 15 years it has commissioned 53 mini-HPPs in different regions and abroad. The total capacity of all commissioned facilities of MKS Group amounted to 244 MW. MKS Group is the official Russian dealer and service partner of MWM Austria GmbH.
© MKC Group of Companies LLC, 2020